At present, it can be said that sheet metal stamping is a kind of processing method with high production efficiency, low material loss and low processing costs. With the advantage of high precision, stamping is suitable for the production for large quantities of hardware processing parts, which could facilitate mechanisation and automation. So what exactly is the stamping process of hardware stamping parts?
Firstly, for general hardware stamping parts, there are four types of processing in the production as follows.
1.Punching: The stamping process that separates the plate material (including punching, dropping, trimming, cutting, etc.).
2. Bending: a stamping process in which the sheet is bent into a certain angle and shape along a bending line.
3. Drawing: The metal stamping process that turns a flat sheet into various open hollow parts or further changes the shape and size of the hollow parts.
4. Partial forming: a stamping process that changes the shape of the blank or stamped part by various partial deformations of different nature (including flanging, swelling, levelling and shaping processes, etc.).
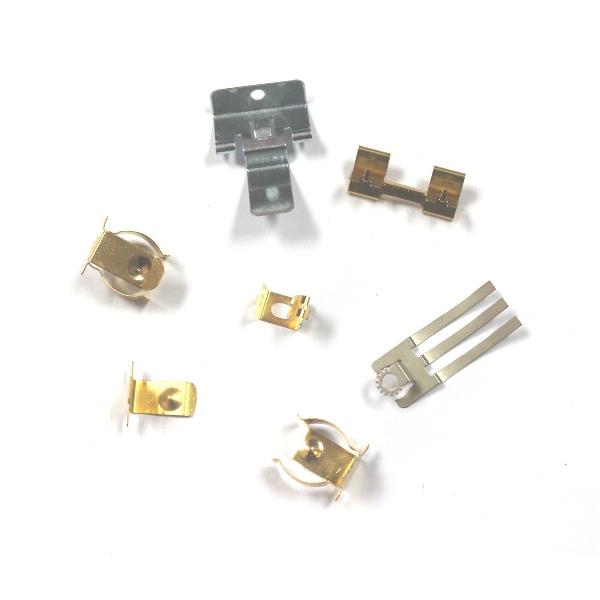
Second, here are the hardware stamping process characteristics.
1.Stamping is a high production efficiency and low material consumption processing method. What’s more, stamping production not only strives to achieve less waste and waste-free production, but also makes full use of the edge remnants even if they are available in some cases.
2. The operation process is convenient and does not require a high level of skill on the part of the operator.
3. The stamped parts generally do not require further mechanical processing and have high dimensional accuracy.
4. Stamping parts have better interchangeability. Stamping process is more stable and the same batch of stamped parts can be exchanged and used without affecting the assembly. They can be exchanged for each other without affecting the assembly and product performance.
5. Since the stamping parts are made of plates, they have better surface quality, which provides convenient conditions for subsequent surface treatment processes (such as electroplating and painting).
Post time: Nov-11-2022